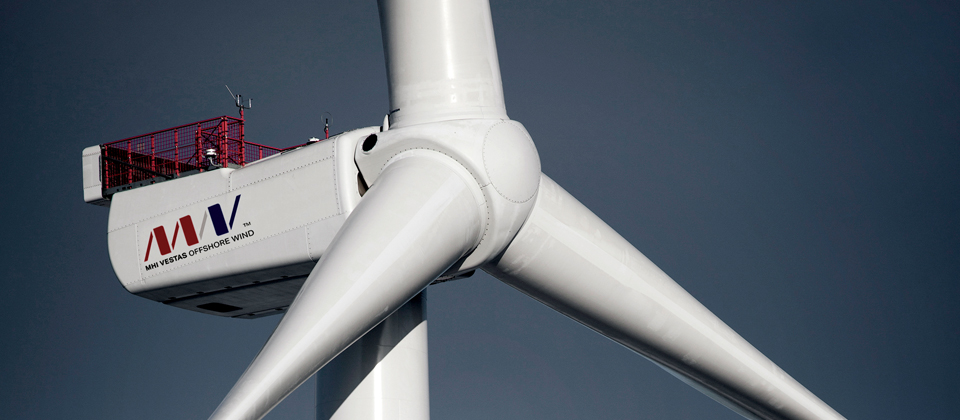
In 2014, DONG Energy announced that the MHI Vestas V164 8.0 MW turbine was the preferred model for Burbo Bank Extension, making it the first commercial site for an 8 MW turbine project. We asked A2SEA’s Hans Peter Johannsen what it takes to load, transport and install these huge structures.
Hans Peter Johannsen, Vice President, Projects at A2SEA, is an old hand in the world of turbine installations. He was there way back when 3.6 MW turbines were the new, big thing – or, for example, the 2.0, 2.3 and 3.0 MW ones that came before them. And he clearly remembers how much rethinking was needed to cope with each step. Now, however, the models of yesteryear look small next to the towering giants of today: the MHI Vestas 8 MW turbines to be installed at Burbo Bank Extension offshore wind farm in 2016.
“From a transport and installation perspective, there’s a lot of similarity between the Siemens Wind Power 6 MW and the MHI Vestas 8 MW,” he says. “We’ve made new sea fastenings, but the basic template is the same – there’s a four-turbine setup on board and we have already improved our crane capacity by extending the boom.”
Dig a little deeper, though, and the differences do begin to surface. To understand them, it helps to have seen more than one installation project in action, but the general principles are relatively simple.
“Blade-handling is completely different, because where Siemens handles its blades individually, Vestas currently plans to load its blades via a cassette that requires two cranes for loading,” says Hans Peter Johannsen.
“In both cases, blades are handled using a lifting tool. But while the orientation is the same, the turning of the blade is different. The Vestas blade is horizontally oriented, whereas the blade for a Siemens 6 MW is vertical because the S yoke (the lifting tool) is lifted down to handle the blade horizontally. The Vestas yoke is more like a forklift in its approach.”
The cassette approach means that for sea fastening, the vessel only requires a substructure into which the cassette can fit. This is in contrast to a Siemens Wind Power blade stack where the sea fastening is a larger structure that remains in place throughout the project, with the blades being moved in and out as required. With MHI Vestas 3.0 MW turbines, cassettes can also be lifted three or four at a time, and comparatively easily stacked on top of each other.
Siemens Wind Power, on the other hand, with its focus on offshore turbines, has optimised the complete handling of each nacelle. A transport frame remains in place underneath the component from the factory to the vessel and out to the site, returning to the factory once the installation is complete. The huge frame has a low centre of gravity, meaning it is very stable on deck even in rough seas.
“Vestas uses a road transportation frame that caters both for onshore and offshore nacelles, so we need to apply a proper sea fastening that uses much more steel than the simple, four-corner castings and a lashing required with the Siemens model.”
Work is underway, however, to design sea transport frames that allowfastenings to be prepared onshore on the frames themselves, enabling them to easily be lifted and fitted into corner castings on board.
“We try to adapt our learnings from the past and bring them into the project,” says Hans Peter Johannsen. “We listen closely to Vestas’ requirements and we’ve had many good meetings where the Vestas team have been open to our suggestions, too.”
Once out at sea, installation uses the same basic type of tools for the 6 MW and the 8 MW turbines. Both turbine manufacturers use wellknown approaches that mean there are few differences in terms of positioning on the vessel, and that handling and installation, while subtly different, are largely similar.
“The towers for the 8 MW are around half a metre wider in diameter, so their additional size and equipment mounted on the side of the tower sticks out a little more, requiring greater distance between them on board, but SEA CHALLENGER is a big vessel, so it’s no real problem.”
Hans Peter Johannsen points to the quality of cooperation at Burbo Banks as a personal highlight:
“When you’re dealing with the market leaders in an industry – large, professional companies that have enormous expertise – everyone works well together, even cooperating between the companies themselves to further develop capabilities. And that’s a key ingredient for success.”
Since Hans Peter Johannsen joined A2SEA in 2008, he has led installations at Horns Reef 2, Rødsand, Baltic 1 (all with 2.3 MW turbines), Gunfleet Sands 1+2 (3.6 MW), London Array and West of Duddon Sands (3.6 MW), and Westermost Rough (6 MW). Today, he heads up all project management for A2SEA and CT Offshore, including the site management, engineering and subsea departments.
Like this post? Subscribe now and get notified about new content!