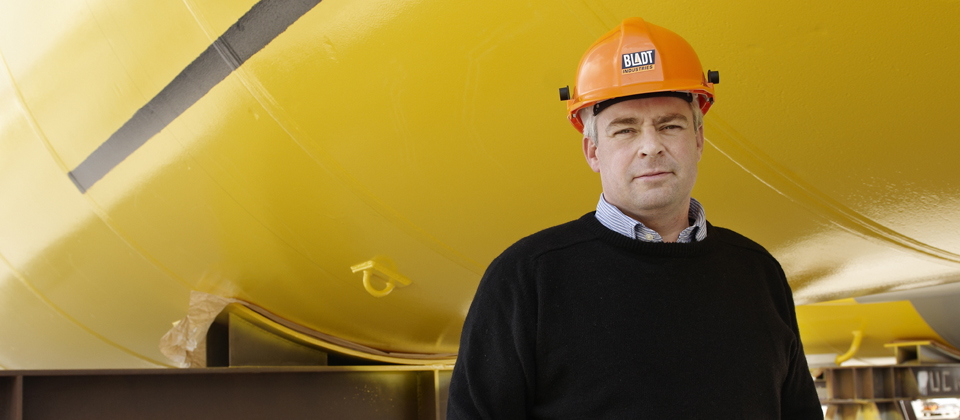
Two leading figures at the forefront of foundation developments speak out on the viability of XL and XXL monopiles.
Monopile foundations have long been the mainstay of offshore wind turbines. Now, with current trends toward larger turbines and deeper waters, the latest XL and XXL monopile designs are bigger than ever. But do these structures make sense? And what do they mean for the supply chain?
Surprise – it’s monopiles!
Director of Business Development, Offshore Wind, Søren Juel Petersen from the consulting engineering group Ramboll is keenly interested in the future of monopiles. “Just two or three years ago, everyone expected that the foundations of larger turbines in deeper waters would be jacket, concrete gravity base or tripod designs. Today, however, XL (for up to 45 meters of water) and even XXL monopiles for 6-7 MW turbines at 40-60 metres of water depth seem to be the way the wind is blowing.”
Bladt Industries CEO, Peter Rindebæk, agrees. His company manufactures steel structures for the oil & gas, infrastructure, and offshore wind energy sectors, supplying monopiles for Horns Rev 2, London Array, Anholt and many others.
”We have so often said: ‘Surely they can’t get bigger’,” he says. “But around 12-14 months ago, utilities started looking into monopiles for even larger turbines and deeper waters. Since then, more have come up with concepts and designs.”
”In fact,” says Søren Juel Petersen, ”we can design any size or weight of foundation. Naturally however, there are some tough fabrication and installation issues. But by evolving, we can see it is possible to produce larger and larger diameters, and it will also be possible to lift them.”
“Producing, transporting and installing such huge monopiles does, however, require supply chain changes,” he warns.
Expensive scale-up
Peter Rindebæk is cautiously optimistic about the production challenges presented by these giant structures. “Basically, we know how to roll the plate and weld it together. But XL and XXL sizes are a cross-industry challenge from the plate mills to the installation exercise. We need to make big investments across the whole production flow to meet these new designs. All our processes have to be re-designed and re-engineered.”
Bladt Industries isn’t the only foundation manufacturer needing to scale up – it’s an industry-wide priority. “It’s hugely expensive, so everyone tends to just scale up to what is required and not beyond. And the consensus has been that things wouldn’t go any further because of the limitations at each step in the value chain.”
One of those limits, according to both experts, is the pile-driving hammer. Ten years ago, 4-metre hammers were considered to be the stopping point. Now a 6-metre monster is underway. Deploying a hammer of this size bears additional risks, but these are likely to be overcome.
Despite the speed of developments, Bladt Industries hasn’t been caught napping. “We’ve already established an expertise and storage facility at Lindø yard (Odense, Denmark) that enables us to invest less than if we had to do it ourselves all from scratch.”
Keeping a lid on costs
Ideally, designing offshore turbine structures is something best done in close consultation among wind farm designers, fabricators and installers. The reality, however, is that such cooperation is still in its infancy. That said, Ramboll says it is increasingly able to conduct more advanced FEED studies with greater involvement from late-phase contractors. Knowing, for example, the equipment used by a fabricator as well as the capabilities and limitations of that equipment may enable designers to achieve better cost-efficiencies.
Both experts point to the availability of suitable installation vessels as a key cost point. With few vessels able to work with XL or XXL monopiles today, and just as few planned or being built in the near future, lack of competition is likely to drive costs upward.
Installation challenges
The list of installation challenges is long, ranging from transport on land and sea, lifting, and driving these monopiles into the seabed.
The latter task isn’t the easiest, either. “We’ve been working with drive-drill-drive installations but, as we increase diameter, it becomes much more expensive to drill,” says Søren Juel Petersen. “Just imagine the cost of a drill with a 7-meter diameter!”
There may be help on the horizon for installation contractors, too. “Theoretically, to reduce the required lifting capacity of large monopile installation vessels we could extend the length of transition pieces – thus reducing pile length,” says Søren Juel Petersen. “But this is, as yet, untested. It’s an underwater connection, which requires divers and bears its own set of challenges. But it’s worth investigating.”
Future prospects
Are super-sized monopiles the way of the future? Like his industry colleague at Ramboll, Peter Rindebæk is convinced they are here to stay. “I don’t think anyone will go back to today’s sizes because it will also mean going backwards in turbine size. And increasingly larger, more efficient turbines are the market driver.”
“The question is how big will the market be and when? Lower numbers over a long period or will everyone go for it at short notice for a demand peak? It’s too early to predict at this stage,” says Peter Rindebæk. “But it’s clear that some utility companies are looking at projects where they expect to use XL monopiles. Currently we are working on 4-5 projects that are leaning in that direction but whether they will all happen is anyone’s guess.”
“It’s not just a question of choosing just one foundation design,” says Søren Juel Petersen. “Instead, it’s about trying multiple layouts or concepts to see what works. For example, we took a project purely designed with jacket foundations and turned as many of the foundations into monopiles as possible in order to reduce costs. And that was a definite success.”
Like this post? Subscribe now and get notified about new content!