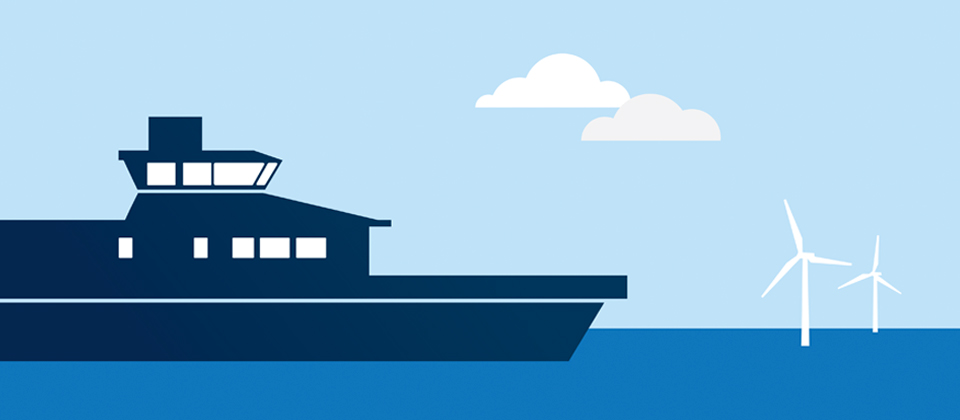
Crew transfer vessels, or CTVs as they are known, are at the heart of the O&M vessel revolution. A2SEA’s offshore wind experts give their viewpoints on prominent CTV issues.
1. SWATH: TRIED AND TRUE
Crew transfer vessels, or CTVs as they are known, are at the heart of the O&M vessel revolution. A2SEA’s offshore wind experts give their viewpoints on prominent CTV issues.
“The SWATH vessels we’re working with have proved their worth and are a workable tool for the O&M work required,” says Vessel Superintendent Pauli Danielsen. “There are always new developments coming along, but this is a tried and proven methodology that most likely already lives up to the regulatory standards of the near future.”
2. HIGH-SPEED SLOW-DOWN
One obstacle to be overcome concerns the IMO’s high-speed craft (HSC) code*. It’s a complete set of detailed requirements for HSCs, including equipment and conditions for operation and maintenance. And it applies to a broad range of vessels. While the code has done much to promote safety in general, it was formulated before the arrival of offshore wind – and it has become a barrier to optimising crew transfer operations. “As it is now, we have to get pre-clearance from the authorities for each route we travel,” says Jesper Tang Kristensen, Technical Development Manager. “We have to describe all rescue points, where we can go to leeway and more besides. And if we move to another wind farm we have to do all that work again. So there’s not much flexibility if it turns out that it would be more time- or cost-effective to deviate from the planned route. And of course, with hotel vessel transfers becoming
more applicable, we could really use a little help here.” Given this situation, the industry is currently looking to the IMO to provide exemptions that would allow it greater flexibility.
3. TECHNOLOGY TRANSFER
“We’re watching a number of technological developments with interest,” says Jesper Tang Kristensen. “Movement monitoring systems, for example, can record every stepover, including weather conditions. So they have a more objective, data-driven basis for reassuring crew that it’s safe to step over – or for identifying high-risk situations.”
“For now, CTVs frequently depart without knowing whether a step-over is possible, so more data could lead to greater efficiency. And some systems can even monitor the pressure against the turbine to show the vessel hasn’t pushed too hard, or provide data on transit conditions to reduce the incidence of sea-sickness for future trips.”
4. SPEED OR RELIABILITY?
“There are different philosophies out there,” says Pauli Danielsen. “Some people are focused on speed – up to 30 knots, perhaps. But our experience tells us that it’s better for the overall project to focus on reliability rather than only on speed. Combined with proper planning, reliable vessels deliver on time, every time – and this is what our customers really want, too. There are some technical trade-offs. For example, the further you are from shore, the more speed becomes a desirable factor. But faster vessels are also lighter, so there are more days where they simply can’t be used due to adverse weather conditions.”
5. LUCKY NUMBER?
How many people should a crew transfer vessel be able to carry? Pauli Danielsen explains that the current practice for normal operations in O&M is to deploy just 3 or 4 teams, with no more than around 12 technicians on board. This allows more time for putting technicians safely onto turbines and picking them up again. More passengers would mean less time on each turbine for each team, and increase idle time across the board. “Every now and then, being able to take up to 24 technicians may be useful, though, when ferrying crew to and from hotel vessels.”
EXPLORING O&M OPTIMISATION
Together with other supply chain participants, A2SEA is part of an Offshore Energy-led project that examines ways to improve O&M efficiency. The project aims to identify the O&M entire process for the planned maintenance of turbines: from early planning, and the morning start, until the technicians have done their job and are safely back in harbour. What are the process steps? Where can time and fuel be saved, better decisions made, better communication achieved? What if, for example, the CTV crew were given a task list the day before the operation so they could give their input to LEAN loading of the vessel, transit route and optimised route in the OWF, for example (at present, CTV crew have little influence on the task once the support vessel leaves the harbour)?
“The project is a good example of how several companies putting their heads together can really pay off. It’s getting a lot of attention from, DONG Energy, Siemens Wind Power, MHI Vestas and Vattenfall, all working together to sharpen our competitive edge,” says A2SEA Technical Development Manager, Jesper Tang Kristensen.
Like this post? Subscribe now and get notified about new content!