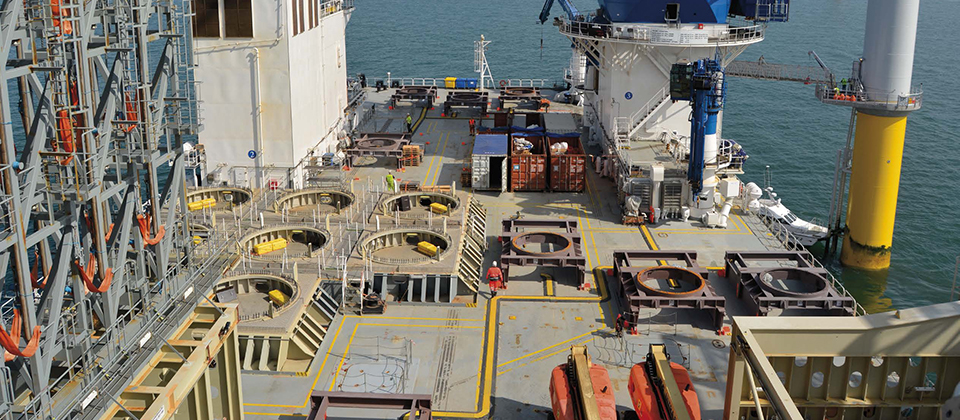
By Glen Andresen
In the wind turbine construction business, few things are as important as deck layout. Get it right and projects can run more smoothly and safely. Get it wrong and you’re likely to waste time and money through inefficiencies that just seem to compound one another – not to mention putting life and limb at risk.
An optimal deck layout makes life easier for everyone. Loading becomes more efficient, transportation more stable, and lifting positions and procedures function like clockwork. And ideally, the same basic layout can be used from project to project, and with as many different types of components as possible.
Recognising the importance of this factor in the construction game, A2SEA’s project management team has been hard at work designing an optimised and standardised layout for SEA INSTALLER in close cooperation with the client and the wind turbine manufacturer. The focus has been on creating a highly efficient setup that works not just for Siemens 3.6 MW turbines but also for their 6 MW big brother.
Optimal layout for an optimal vessel
To begin with, of course, SEA INSTALLER’s crane placement and free deck plan are ideally suited to turbine transport and installation. With instant manoeuvrability, a deck built to withstand massive loads, a leg center-installed crane that can slew 360 degrees without encountering another leg, extended crane reach and many other advantages, SEA INSTALLER is already a solution that’s hard to beat. She’s even prepared for future lift capability upgrade to 900 tonnes.
But there’s always room for improvement
Achieving an optimal deck layout demands both deep and broad knowledge covering everything from principles of vessel architecture to experience with hands-on lifting operations. The end goal is to determine exactly where blades, towers and nacelles are best positioned in relation to the vessel and to each other, in order to smoothly facilitate loading, transport and lifting, while keeping a watchful eye on safety aspects for the vessel’s crew and contractors. Getting it right takes years of experience and more than a little creativity.
The new layout is characterised, for example, by the grouping of towers, blades and nacelles in distinct areas. This is in contrast to the usual practice of trying to make maximum use of the space on deck by placing different types of components “mixed together” throughout the deck space. Another rather obvious difference is in the way the blade rack is centered such that the blades protrude both to port and starboard. Normally, blades protrude on one side of the vessel only. But more on that later. First, let’s examine the benefits of this unusual layout.
Loaded with advantages
While the layout has most of its benefits during the installation phase, there are a few loading advantages, too. One of these is the ability not to perform simultaneous lifts, but to be able to prepare for the next lift (such as hooking a crane up to the next component) before the preceding lift is completed. What makes this possible is the distance mentioned above between dedicated component areas on the deck. So it is possible to reduce loading time to some degree.
Another area of advantage is sea fastenings. Again thanks to specific, dedicated areas for each component on deck, we have been able to standardise the design of sea fastenings rather than requiring a different fastening (such as a specially constructed bracket) for the same component at varying deck locations.
Stability of the vessel is also enhanced. Typically, with a full complement of components on board, there’s a lot of load at the aft end of an installation vessel, requiring vast amounts of ballast water as a counter weight. With the new deck layout, however, the load is distributed more optimally around the vessel’s centre of gravity, requiring less ballast water and reducing structural stress.
Related to the issue of stability, but also to the vessel’s ability to sail in a variety of sea conditions is the way in which the new layout calls for the blade rack to be centered such that blades protrude both port and starboard. Doing so reduces the likelihood of blade tip immersion (waves touching the blades) in higher sea states, enabling the vessel to confidently sail in adverse conditions.
Sticking with the same basic deck layout makes mobilisation somewhat easier, too. With, for example, towers and their foundations concentrated in one deck area and nacelles in another, multiple teams can work simultaneously, each focusing on their particular component type. With such clear delineation, each operation becomes safer, despite the fact that there may be more than one lift being performed at the same time.
Perfect positioning
But perhaps the best aspect of SEA INSTALLER’s optimal, standardised layout is the way in which it enables on-site installation. And an important part of that puzzle involves the positioning of the gangway in relation to the transition piece. Towers, for example, placed far from the nacelles on the starboard side, don’t present the usual boom conflicts that can make lifting nacelles a delicate task.
Moreover, with the blades positioned forward, there’s more free space at the aft end where the transition piece is located, approximately 20m from the vessel. The blade rack is both high and wide, which means that if it were placed aft it would be likely to come too close to the transition piece. As a result, lifts seldom take place above the gangway except, of course, for final tower lifts onto the transition piece.
The Siemens installation team on board SEA INSTALLER also benefits from the optimised deck layout. Their office is located adjacent to the gangway – and with fewer lifts over the gangway area, they now have greater access to the turbine being installed as well as a better overview of operations from the office.
Everybody wins
All in all, the new standardised, optimised deck layout makes significant savings possible, reduces mobilisation and sea fastening tasks, and offers safety benefits at the same time. And it adds value not just for the client, but also for the turbine installation team and A2SEA.
Like this post? Subscribe now and get notified about new content!