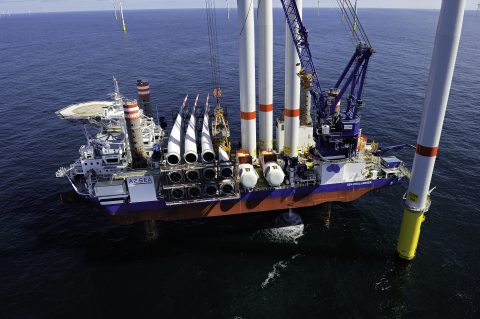
By Hans Peter Johannsen, Vice President, Projects.
This is the first post in a series about reducing the LCoE in the offshore wind industry through optimising turbine loading, transport and installation.
In offshore wind, few things dominate industry conversations as much as reducing the levelised cost of energy (LCoE). And certainly, with many years spent working to optimise equipment, procedures and safety, turbine installation contractors such as A2SEA have been able to become highly efficient, bringing the costs of installation down within the installer’s scope of control. In a series of articles, we’ll be discussing the steps we’re taking to achieve even greater efficiencies.
Optimisation advantage
Overall, the whole setup on both substation, cabling, foundation and turbine installation – the whole planning of the sequence between tasks – needs to be optimised and we are only a small but vital piece of that. But it’s quite a standardized operation (all the turbines are more or less the same).
When discussing how turbine installation contractors can contribute to reducing the LCoE, it’s important to realize that, in many ways, we have a uniquely privileged position in the supply chain: Unlike foundation installation, where everything differs (water depth, soil conditions, types of foundation, etc.) or cabling works, we deal with the relatively repetitive installation of quite standardised components, giving us plenty of chances to constantly improve the way it’s done.
In fact, as we will reveal in this article series, a turbine installation contractor worth its stuff can often move faster and more efficiently than other parts of the wind farm construction system.
Sharing the know-how
That doesn’t mean, of course, that we can simply sit on our hands and wait for the rest of the supply chain to catch up. Instead, we spend a lot of time discussing ways to help speed things up beyond our own functional area (with an eye on safety, of course!) – and, of course, we share those thoughts with turbine manufacturers, assemblers, load-out contractors and anyone else we think may benefit.
If bringing down the LCoE, at least in terms of turbine installation, were only a matter of optimising basic processes, it would be a simple world indeed. The reality is, however, is that there are other forces that impact on how much a turbine installation contractor can focus on efficiency alone. And one of these is risk management.
Combatting the costs of risk management
Wind farm developers are, naturally, interested in making the installation of foundations, turbines and all the other project aspects as smoothly predictable as possible. A lot of effort, therefore, goes into predicting and mitigating delays, whether due to the weather, for example, or to equipment failures.
Working together with the client following the awarding of a tender, a turbine installation contractor negotiates where to arrange for contingency and redundancy. The less risk the client wants to bear, the more expensive turbine installation becomes.
This then, is another area where we apply expertise to come up with creative solutions that can offer contingency and redundancy for the lowest possible cost. At one end of the scale one could imagine, for example, a stand-by vessel, backup crew and multi-scenarioed operational plan. But these are hardly the most cost-efficient solutions. Instead, we focus on equipping our vessels, sharpening our procedures and carefully planning transport and installation operations to reduce risk and enable the flexibility required if and when things don’t go to plan.
The next post in this series explains how the LCoE of turbine installation can be reduced by upgrading existing vessels to handle taller, heavier turbines.
Like this post? Subscribe now and get notified about new content!